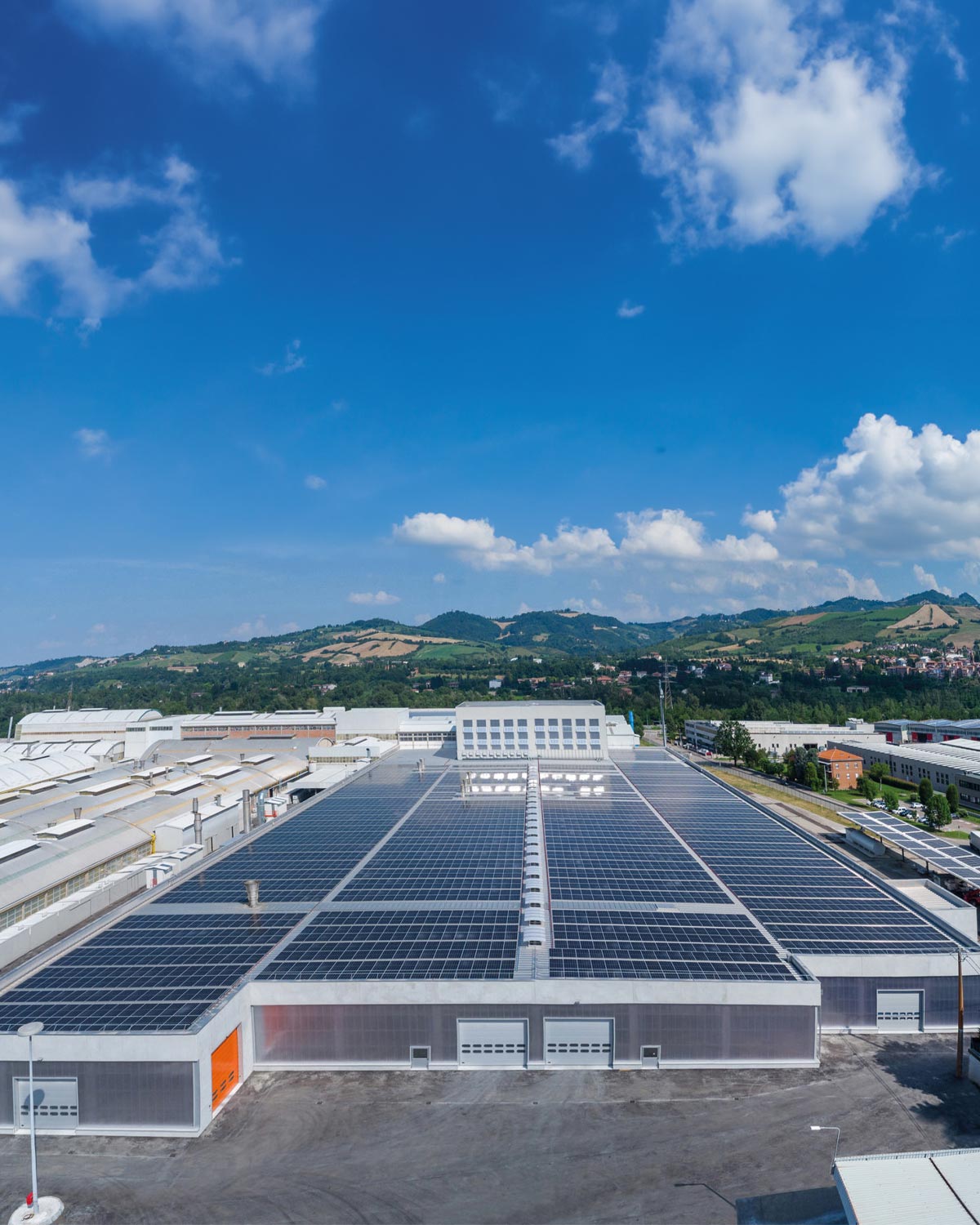
WE ARE SHAPING THE FUTURE OF THE CERAMICS INDUSTRY WITH THE WORLD’S FIRST FACTORY POWERED BY GREEN HYDROGEN
Castellarano, Reggio Emilia, is home to the world’s first ceramics industry powered by green hydrogen: a project representing yet another of the Company’s concrete actions that continue to work for a more sustainable future. With this new production site, Iris Ceramica Group is creating a new manufacturing standard creating an industrial process with no baseline for comparison and paving the way for a unique model that will become a cornerstone.
This is the first concrete and innovative project to decarbonise the Italian ceramics industry using green hydrogen.
An initiative that paves the way for the decarbonisation of a hard-to-abate sector, decisive for achieving the energy transition objectives of the country and a strategic area for this industrial district. Skill, innovative technologies and the solid determination to believe in a virtuous path towards decarbonisation are just some of the key elements put into play to bring life to the first ceramics industry running on green hydrogen.
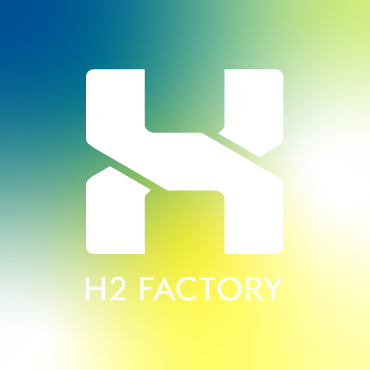
THE NAMING
The green hydrogen-powered ceramics factory has a name and an unmistakeable iconography: H2 Factory® is the Proper Name chosen to uniquely define the first example of industrial eco-innovation in the ceramics sector. The H2 FACTORY® logo is deliberately shaped in an industrial style, and the colours chromatically represent the choice of using renewable sources: solar energy combined with rainwater translate into the yellow and pale blue that together create green: green hydrogen.
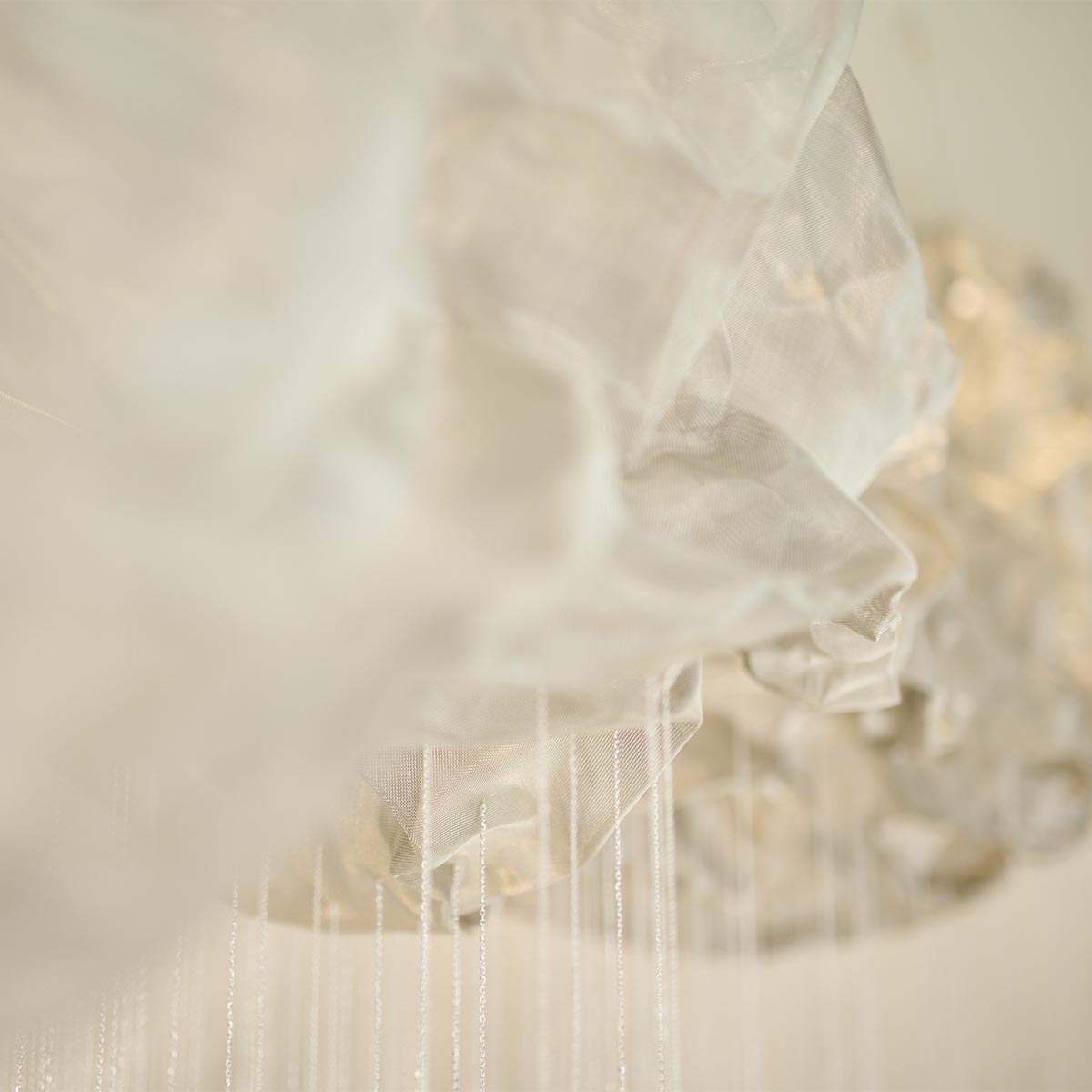
THE “CLOUD TO CLOUD” CIRCULAR PRODUCTION PROCESS
The hydrogen journey starts far, far away, from the stars and reaches the Earth through solar energy stored in photovoltaic panels installed on the factory roof.
At the same time, rainwater is collected and subjected to electrolysis – in an electrolyser powered by electricity obtained from solar panels - to separate the hydrogen from the oxygen. “Freed” in this way, the hydrogen rises and is conveyed to power the factory, especially the kilns. When the ceramic slabs are fired, the hydrogen and oxygen in the air are recombined, returning to the atmosphere in the form of water vapour, recreating the clouds they were generated from.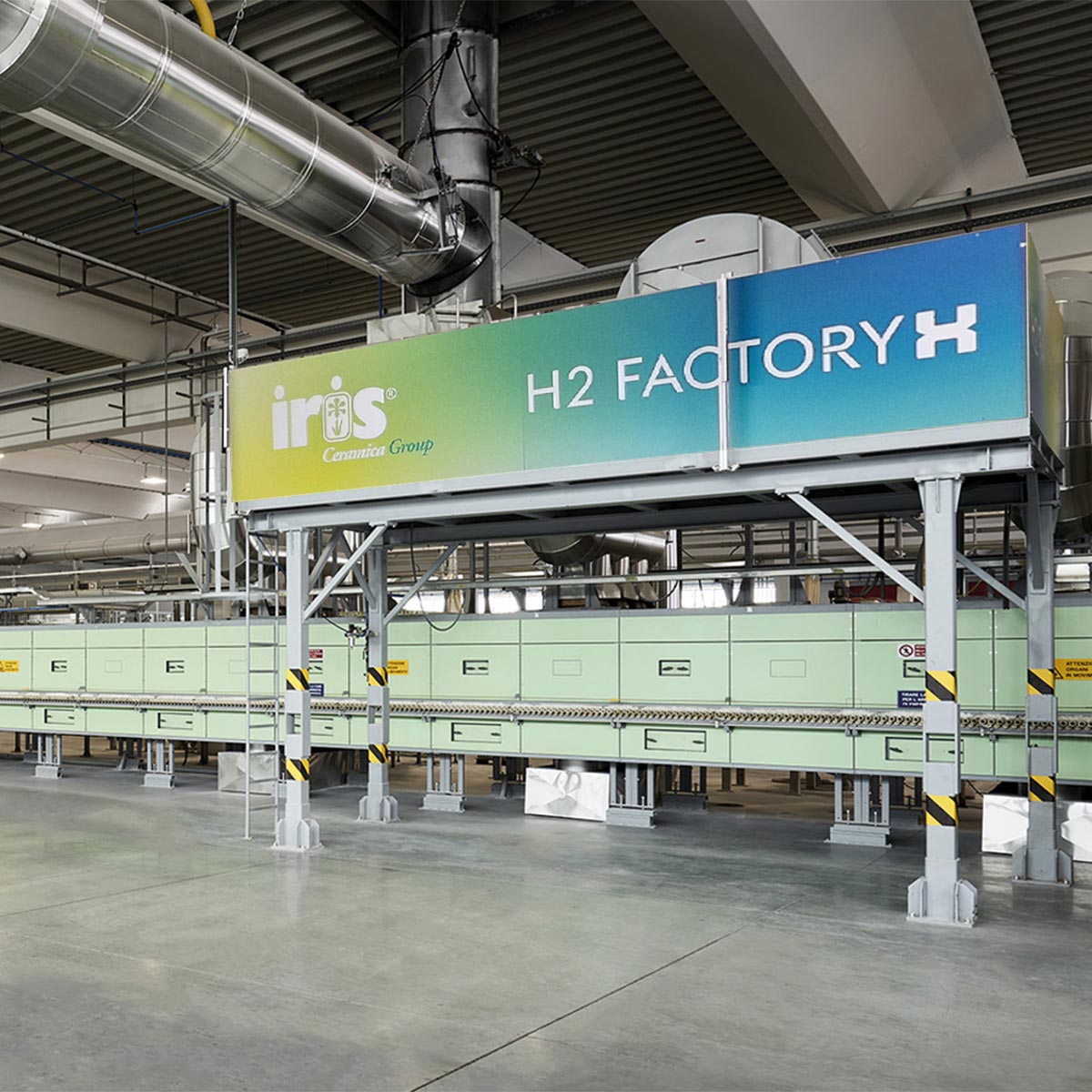
IRIS CERAMICA GROUP WITH EDISON NEXT
The H2 Factory® has become reality through the agreement with Edison Next, made official in July 2023, through which Iris Ceramica Group has developed a pioneering, bespoke production process. For the H2 Factory®, Edison Next will develop a 1 MW capacity plant for the production of green hydrogen using electrolysis, powered by renewable energy. The electrolyser will use rainwater withdrawn from collection tanks, thus fostering virtuous water management, consistently with the principles of the circular economy.
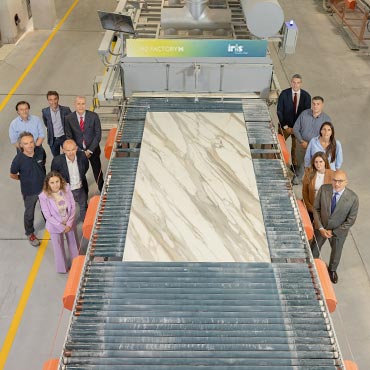
THE FIRST SLAB
In July 2024, the world’s first 4D Ceramic slab was produced using a mixture of green hydrogen – hydrogen obtained using renewable energy – and natural gas. Specifically, the produced slab is 3.2m long, 1.6 metres wide and 12 mm thick, and stands out for its four dimensions – which gives it the name 4D Ceramics - in which in addition to the three-dimensionality of the material and its grains, which cross the whole thickness of the slab, we find the fourth dimension of sustainability. Several preparatory activities have been completed in order to launch this first phase: the civil works to prepare the area, the installation of the blending unit, which is the system that mixes the natural gas with the green hydrogen, and all the connections required between the different equipment. Furthermore, a 1.3 MWp photovoltaic system has been installed, in addition to the existing 2.5 MWp plant. In particular, the H2 pilot production plant, in operation since May 2024 for the test phase, includes two temporary electrolysers with a total power of 120 KW, powered by renewable energy. The two electrolysers, installed in a container, can produce up to 20 cubic metres of green hydrogen per hour, powering the new, latest-generation “hydrogen ready” kiln with a blend of green hydrogen up to around 7%; this percentage will increase once the final plant is installed.